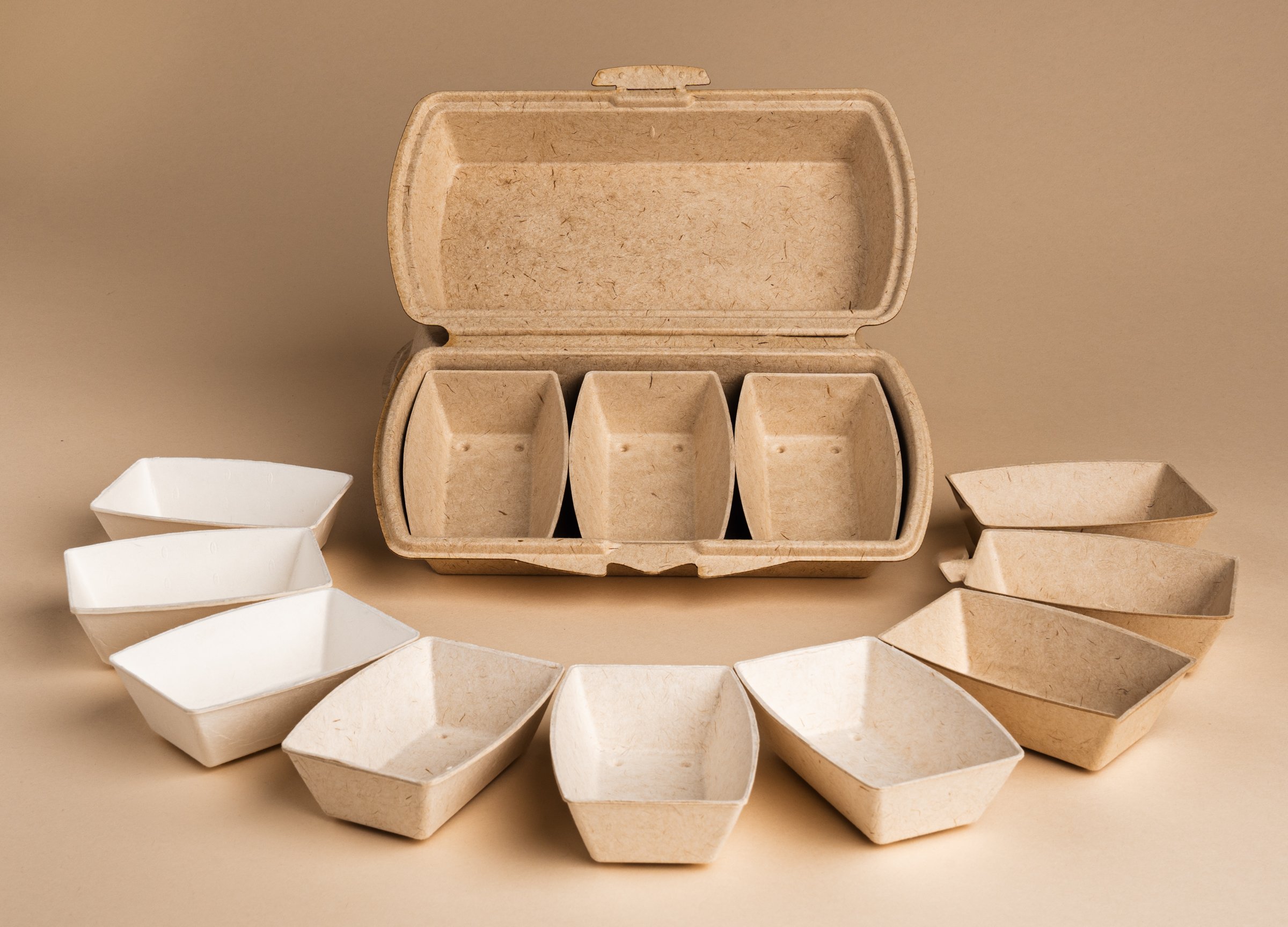
Molded Fiber 101
Definition
Molded fiber is the process of taking a fibrous material and molding it into a strong, resilient shape.
Manufacturing Types & Processes
Type 3 & Beyond
Tanbark specializes in Type 3 molded fiber, also known as encapsulated drying. The formed product goes through a series of heated, high-pressure molds, delivering a product that closely resembles the appearance and functionality of thermoformed plastic.
This process provides highly detailed surface finishes and complex designs with strong yet thin walls. Leveraging decades of experience, Tanbark is pushing the boundaries of type 3 production, as well as building “type 4” capabilities with further processing like die cutting and labeling.
Type 1
The simplest and oldest process, Type 1 molded fiber uses a single mold to form a part from a pulp slurry, which is then dried. This results in a rough, thick-walled (3/16”-1/2”) product with only one smooth surface. Typical applications include mostly industrial and appliance packaging, as well as flowerpots and plant containers.
Type 2
Type 2 molded fiber adds a transfer tool that slightly reshapes the formed part before oven drying. The results are a thinner (1/8”-3/16”) part with one relatively smooth surface and one rough. Typical applications are the four-cup coffee carriers and egg cartons.
Sustainable Sourcing
Many sources can be used for molded fiber–wood pulp, grasses, and even recycled paper. We commonly use locally sourced virgin wood fiber. Maine’s heritage industries, Forestry, Lumber, and Molded Fiber, support abundant, natural forests: sustainable forestry provides logs for the sawmill while smaller residuals are used for hardwood and softwood pulp. This business ecosystem supports Maine’s Forest economy–maintaining a strong community, natural habitat, and recreational opportunities, all while sequestering millions of tons of CO2 each year–a working forest is the best carbon capture machine in the world.
From Pulp to Product
With our sustainably sourced raw materials, we guide you toward the best fiber blends and necessary additives to develop a custom recipe that meets your end-product needs.
Fiber Selection
A series of large tanks, pumps, and lines allows for efficient management of both pulp processing and water recapture. This close-looped system, called the wet end, directly feeds the former machines.
The “Wet End”
Forming machines use encapsulated drying, where pulp slurry is drawn onto a porous tool, then transferred to heated pressing and drying tools that shape the product and capture and recycle water vapor.
The Formers
Designed with Intent
We look at every project as an opportunity for improvement. Whether you are starting from scratch or converting an existing product, we strive to fully understand the application and context, working with you and your team to optimize the design. The aesthetics, functionality, and product lifecycle are all taken into account so that your new fiber product not only meets your sustainability goals, but improves satisfaction across the board.
Partners
Circular Life Cycle
Biodegradable
Molded fiber products naturally break down into organic matter, minimizing both environmental waste and impact.
Recyclable
Molded fiber made from wood can be recycled like paper after use, often being used to make more molded fiber parts. This closed-loop process supports sustainability and helps lower landfill waste.
Compostable
Molded fiber decomposes in composting environments, turning into nutrient-rich soil within a short time. You can offer a zero-waste product, leaving no harmful residue behind.
Curious to learn more?
Contact us with your molded fiber product inquiries.